Customer
Founded in 1985, Hengan Group is currently the largest manufacturer of tissue paper and maternal and child hygiene products in China. It was listed on the Hong Kong Stock Exchange on December 8, 1998. On June 7, 2011, Hengan International was included in the Hong Kong Hang Seng Index constituents.
Hengan owns four well-known Chinese trademarks, Anerle, Xinxiangyin, Seven Degrees Space, and Anerle, and its three leading products, sanitary napkins, diapers, and household paper, rank among the top in domestic market share.
The group has 14 production bases in Fujian, Shandong, Hunan and Chongqing.
Project
The Hunan Hengan project is located in Changde, Hunan. The project invested 819 million yuan to build a 36,000-square-meter paper workshop and a 24,000-square-meter storage center. In March and May 2023, two new state-of-the-art paper production lines will be installed. After completing 6 phases of investment, the annual production capacity of base paper will reach 345,000 tons, and the annual processing capacity of finished products will reach 28 million boxes.
In July 2023, Hengan (China) Hubei T31/33 project PM31 paper machine started up smoothly. Yunda supplied stock preparation and approach flow system equipment,including chain conveyor for pulpe bales,high density cleaner, PM double disc refiner, NLS flow screen, broke pulper, etc. The 3600mm width new-moon type tissue machine of this project is supplied by TOSCOTEC, The reliable quality of Yunda stock preparation equipment ensures the smooth runnability of this tissue machine and the high quality of the product.
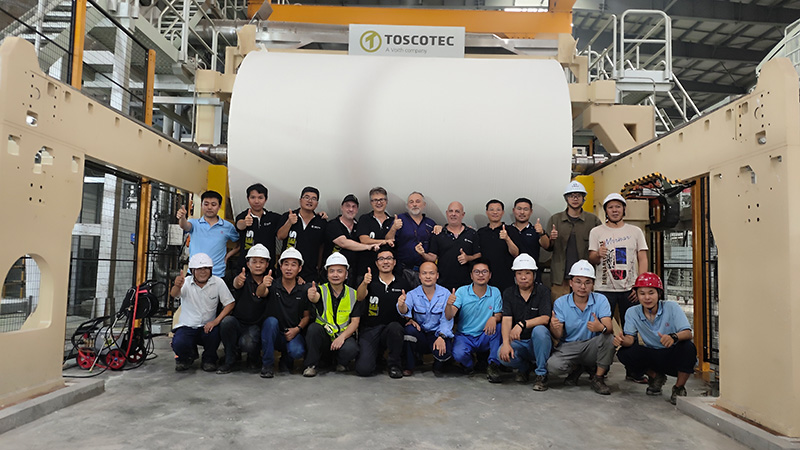
Tissue machines are supplied by TOSCOTEC. Email: info@yundapm.com Yunda supplied the stock preparation and approach flow system equipment including: Chain Conveyors for pulp bales, High Density Cleaners, PM Double Disc Refiners, NLS Inflow Screens, Broke Pulpers, etc. All equipment was started up successfully at one time under the supervision of Yunda’s on-site erection and commissioning service engineer, which was highly recognized and praised by the Production Manager Yang Shikun and the Equipment Manager Hu Zhenglong. Customer expressed their high recognition of Yunda and its equipment.